La filial del grupo Polpaico es la única plataforma en Chile que transforma residuos sólidos industriales en combustibles alternativos para su coprocesamiento, evitando que los desechos que no pueden ser reciclados lleguen a vertederos. El producto es utilizado como energía sustentable en los hornos de cemento de la planta Cerro Blanco, en reemplazo del combustible tradicional.
En un contexto marcado por el calentamiento global, Coactiva, filial del grupo Polpaico, es la única plataforma en Chile que transforma residuos industriales en combustibles alternativos sólidos. A través del coprocesamiento, la compañía evita que aquellos desechos que no pueden ser reciclados, como cosméticos, fármacos, tabaco, fitosanitarios orgánicos, entre otros, lleguen a vertederos y los transforma en energía sustentable que utiliza en los hornos de cemento de su planta Cerro Blanco.
En quince años de funcionamiento, Coactiva a través de su combustible alterno sólido derivado de residuos ha contribuido a lograr una sustitución energética del 13% del combustible fósil tradicionalmente usado, y hoy trabaja alineada a las metas corporativas de sostenibilidad para para aumentar dicha tasa de sustitución hasta un 30% hacia el año 2025, anunció su gerente, Oly Chirino. “Tenemos una meta muy desafiante, que nos permitirá proyectar a la compañía de manera sostenible en el tiempo y contribuir a una gestión más eficiente de los residuos industriales, como parte de nuestra responsabilidad medioambiental”, afirmó.
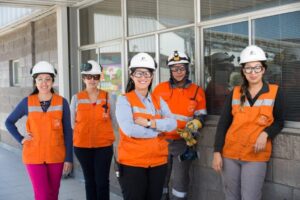
Coactiva gestiona un promedio de 25 mil toneladas de residuos al año, los que provienen de distintos sectores industriales, como billetes que salen de circulación; productos de la industria de alimentos y cosméticos vencidos o que están por vencer; residuos que son decomisados en el aeropuerto por el SAG; insumos médicos, material proveniente de laboratorios farmacéuticos, entre otros. En todos estos casos, el coprocesamiento es una alternativa intermedia entre el reciclaje, la incineración, el vertedero o relleno de seguridad, que implica ahorrar energía, reciclar materiales y reducir el impacto ambiental. En ese sentido, es una opción sustentable para todas aquellas empresas responsables con el medio ambiente que se han impuesto metas ambiciosas por no llevar sus residuos a estos lugares, así como para la generación de combustibles alternativos en la producción de cemento.
Hoy la filial de Polpaico está estudiando distintas tácticas y alternativas para la incorporación de neumáticos en el proceso de coprocesamiento, dado su nivel energético relevante: un kilo de neumático equivale a un kilo de carbón. “Además, como tiene caucho natural, tiene un componente de 20% o más de carbono neutral”, añadió Oly Chirino.
De acuerdo con las cifras publicadas por el Ministerio del Medio Ambiente, en Chile se generan más de ciento treinta mil toneladas de NFU cada año, de las cuales sólo un 17% tiene algún tipo de manejo sustentable. Sin embargo, el restante 83% de los NFU generados cada año no tiene destino conocido, lo que constituye un problema ambiental que, con una regulación adecuada, puede convertirse en una gran oportunidad para aprovechar el valor material y energético de los NFU.
En este contexto, actualmente se encuentra en revisión en Contraloría el Proyecto de Ley de Responsabilidad Extendida del Productos (REP) sobre los Neumáticos Fuera de Uso (NFU), que establece que hasta un 40% de neumático de las 135.000 toneladas de NFU que se generan anualmente en Chile pueden utilizarse para fines energéticos.
“La implementación de esta ley, que esperamos sea a partir del próximo año, es esencial para el cumplimiento de nuestra estrategia y así, alcanzar nuestra meta del 30% hacia el año 2025. La fabricación de cemento es un proceso industrial intensivo en el uso de energía, por lo que, en muchos lugares del mundo, las fábricas de cemento utilizan neumáticos fuera de uso –ya sea enteros, trozados o granulados– para complementar su combustible primario en los hornos de Clinker. Las altas temperaturas y largo tiempo de residencia del combustible en el horno permiten la combustión completa del neumático, sin generar humos, olores o emisiones visibles causadas por los NFU”, aseguró la gerente de Coactiva.